Another shortage? Here’s what is happening to supply chains
Not a day goes by without us hearing about a new shortage: We all remember the trouble finding toilet paper, recently limited infant formula became a supply chain crisis and now there is a shortage of tampons.
But that’s not all.
Contrast dyes for medical imaging scans, Sriracha hot sauces, and helium are among the more arcane ones that I have heard about lately. So, how should we think about what is happening to supply chains? While it seems that a broad range of goods is suffering in one way or another, we can categorize the problems into a few buckets:
Sudden shifts in demand patterns are hard to keep up with
The pandemic ushered in large changes in demand patterns. More sweatpants, less dress clothing. More major appliances purchases and more cooking at home, less restaurant dining. And these patterns are reversing now, so once again that is driving another round of shifts in demand. The problem is that many products have long production lead times — the time it takes from when a company puts the plans in place to make a product until it emerges from the factory and is shipped to stores.
This lead time might be a year or more for shoes or consumer durables — possibly longer for some items and less for others. It takes a while to respond because you need the production line in place, the raw materials ordered and delivered and the workers available; you might not be able to just add more capacity quickly. The problem is the time mismatch between rapid shifts but slow responses. The breadth of the disruption was also unprecedented, so that meant a lot of shifting capacity across the board. Meanwhile, consumers waited.
In some cases when demand dropped, capacity was shut down
Sometimes we just have less manufacturing capacity for a product than we did a few years ago. If you were running an oil refinery during the pandemic, you saw demand drop for gasoline by 14 percent and diesel by 8 percent in 2020. Five domestic refineries, with a combined capacity of over 800,000 barrels per day were permanently shut down as a result. That dropped domestic capacity to a level below what we had in 2016. Globally, 1.6 million barrels per day of capacity were shuttered with only 850,000 of new capacity coming online, the first overall drop in 30 years according to the International Energy Agency.
The last big new domestic refinery was Marathon’s Garyville, Louisiana facility which came online in 1977. With the energy transition looming, investors are likely reticent about building any new capacity. So, when everybody finally decides to commute to work again or take driving vacations, we have capacity shortfalls and prices go up. That’s even before the cut-off of Russian crude oil supplies. And there’s an additional complication — refineries are geared to process certain types of crude oil, depending on things like how “heavy” they are, how much sulfur they contain, etc. So capacity is not readily interchangeable. And that impacts just about everything, because trucks and trails use diesel fuel to move goods around.
In other cases, demand stayed the same or grew, but capacity still came out of the system
This is a major part of the story behind the infant formula shortage. Abbott Nutrition’s factory in Sturgis, Michigan represented a good chunk of domestic capacity. If you take that much production capacity offline for four months, you will inevitably get shortages. We saw the same problem when some meat packing plants shut down early in the pandemic.
That’s also the story on helium. In mid-January a leak at the Cliffside helium enrichment plant in Texas caused a four-month outage, sidelining a source that usually produces 14.2 million cubic meters a year. Separately, a fire at a new natural gas processing plant operated by Gazprom in the Russian Far East took out another 49 million cubic meters of production. On top of that, Qatar shut down two of its three liquefied natural gas (LNG) plants (that extract helium as a byproduct offline) earlier this year for scheduled maintenance. No wonder there is a shortage. Earlier in my career, I actually worked with a lot of liquid helium to cool superconducting magnets, so I appreciate how critical this particular commodity is.
Then there’s hoarding or “just in case” inventory
If you are worried that something that you really need on a day-to-day basis is going to be in short supply, you might buy a little more, just in case. This was the story with toilet paper — Americans bought 700 percent more toilet paper than usual in March of 2020. But they certainly didn’t use 700 percent more toilet paper. Who knows how many people actually stocked up to that extent, but no manufacturer could keep up with that demand surge. While not as visible, it was just as bad in a number of other industries. For example, it appears that many manufacturers were buying twice as many electronic microchips as they needed.
What then is the story on tampons?
I had to research the story on tampons, since I really know absolutely nothing about this particular supply chain. So, I called up Wendy Tate, who is a professor of supply chain management at the University of Tennessee. She told me there was one factory in the Southeastern U.S. that was having trouble getting enough people to staff its third shift. That’s one-third of their capacity. Okay, like me, she wonders why demand has gone up for the hygiene product that, much like toilet paper, should be relatively stable and predictable. “There’s no excuse for demand variability, and yet there are shortages,” she told me. I asked her if she thought hoarding was going up. “I have no idea, but there has been a significant increase in the demand for these feminine care products in the last several months,” she replied.
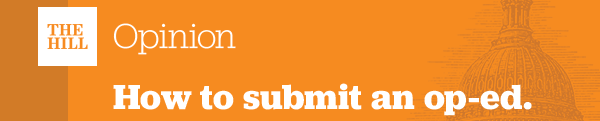
And there’s the dilemma at the heart of this problem. If I “cooperate” with fellow shoppers and don’t hoard, maybe there will be enough of an essential product to go around for everyone. But if I am worried that I may run out, maybe I’ll just buy a little extra. If everyone buys a little extra, stores start to run out while manufacturers rush to respond. In the meantime, when other shoppers get word that they better stock up, everyone runs out and buys everything they can find. Ultimately, everyone has so much stocked in their cabinets that they stop buying, and then demand falls off a cliff. It happened in toilet paper, maybe it will happen here.
Now, about that Sriracha hot sauce linked to an ongoing chili pepper shortage and drought — that’s probably in still another bucket.
Willy C. Shih is the Robert and Jane Cizik professor of management practice at the Harvard Business School. His research focuses on global manufacturing and supply chains. Follow him on Twitter: @WillyShih_atHBS
Copyright 2024 Nexstar Media Inc. All rights reserved. This material may not be published, broadcast, rewritten, or redistributed..