US leaders can help win the EV battery race
The electric vehicle (EV) revolution has arrived, and automakers are racing to take the lead in next-gen battery technology, especially as gas prices skyrocket for traditional vehicles. Automotive manufacturers are investing billions of dollars in new, fully electric vehicle models as new options to their lineup. These vehicles offer owners less interior noise and vibration from the power train, convenient fueling at home, a lower operating cost, and zero tailpipe emissions when the vehicle operates solely on its battery, according to the National Research Council.
This historic automotive shift represents a tremendous opportunity for businesses at every level of the value chain that produce key products, especially lithium-ion batteries, which power most EV vehicles. As with any new emerging industry, there will be changes in technology, which present profound challenges and opportunities related to system performance, durability, safety and cost.
Technology advancements are allowing the next generation of EV batteries to be more affordable, safer, increase driving ranges, and quicker to charge. But some of the critical components that make up lithium-ion batteries aren’t readily available in the U.S. As a result, companies are trying to tap into the world’s production and refinement capacity for lithium, cobalt, nickel, and manganese — critical minerals for multiple lithium-ion battery chemistries.
Why should the U.S. care so much about EV batteries and U.S. manufacturers sourcing locally?
A competitive, domestic battery manufacturing supply chain reduces economic vulnerabilities from reliance on imported materials and offers new prospects for economic growth, recyclability and national security by supplying EV battery materials and components to global markets.
Today, U.S. automakers turn to foreign suppliers because they can’t rely on the U.S. supply chain to ensure they’re getting the materials they need, when they need them.
The EV battery supply chain, from necessary minerals mining and processing to cell and battery manufacturing to battery recycling, includes capital intensive activities with high upfront costs — costs that are often significantly higher in the U.S. than in other countries.
To counter these challenges, the U.S. needs significant new tax incentives to drive the domestic battery supply chain. New incentives would not only help the country realize the full potential of this market, but also will grow the domestic supply chain and help the U.S. lead the world in developing this critical sector.
Federal tax incentives would enable establishment of a foothold domestically to compete with more well-established players globally. Investment Tax Credits (ITCs) and Production Tax Credits (PTCs) have been successful tools to promote investment in U.S. renewable power like solar and wind, fueling exponential growth in these sectors. The U.S. EV battery industry is now primed for such growth.
According to a study by UC Berkeley Goldman School, over 2 million jobs will be realized through 2035, spurred by expanded manufacturing and $1 trillion in consumer savings that the electric vehicle transition will bring.
The EV transition will also lessen U.S. dependence on petroleum with a higher fraction of miles being fueled by electricity. This also means that the amount of carbon dioxide and other air pollutants emitted into the atmosphere would lessen as well. In fact, a series of authoritative scientific reports stress that the emission of GHGs is contributing significantly to global warming, as light-duty vehicles were responsible for 17.4 percent of total U.S. GHG emission in 2012, according to the National Research Council.
Technology companies are racing for their share of the EV market. And upstream suppliers to the automakers, like PPG, will also realize the benefits of a stronger U.S. supply chain. PPG’s broad-based coatings materials expertise covers virtually every area of lithium-ion battery design and construction, helping boost performance, extend service life, improve safety, increase manufacturing throughput, and reduce cost per kilowatt hour — while eliminating potentially hazardous traditional materials like N-methyl pyrrolidinone (NMP).
Policy changes can also enable improved recyclability and reuse of lithium-ion batteries, reducing end of life waste management concerns. Today, according to an article published by the National Academy of Engineering, lithium-ion batteries, while less toxic than traditional batteries, still can have negative impacts on the environment through resource depletion and risks of land and groundwater pollution. Therefore, improved infrastructure for resource recovery is crucial to deliver success. Creating standards across the industry, incentivizing processors, and ensuring strong streams of batteries are all necessary steps for our legislators to make.
Electric vehicle demand and acceptance will only continue to grow. For example, in California, a state that has been leading the transition to EVs, new car sales data show that about 12.4 percent of vehicle sales in the state in 2021 were electric, compared with 3.75 percent in the U.S. overall, Barron’s reported. And the number of light-duty EVs on U.S. roads is estimated to increase 10-fold to 18.7 million by 2030 (up from 1.8 million in 2019). Ward’s Intelligence reported that one in four cars delivered globally in March 2022 was an electric vehicle.
In addition to California, other states like Washington, Oregon, Georgia, Maryland, Vermont, and Hawaii have strong EV markets. According to National Research Council, these markets have been driven by social sentiment, financial incentives, and regulatory mandates for reducing carbon emissions. By continuing to offer tax incentives, toll reduction, free parking, and other forms of fee reduction, the EV market will only grow stronger, especially as public and workplace charging becomes more readily available.
And while we are pleased that the bipartisan infrastructure law includes $7.5 billion to build out a nationwide network of 500,000 electric vehicle chargers, according to the U.S. Department of Transportation, accelerating the deployment of a charging network as the largest U.S. investment in EV charging and contribution to a zero-emission future, it’s not enough.
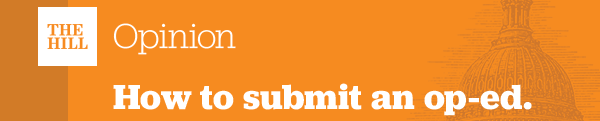
We must establish a strong, reliable and flexible EV battery supply chain.
It is essential to our Nation’s future and our energy, environmental and economic security. And we need U.S. lawmakers to take action now, regardless of political affiliation and implement federal tax incentives. It is essential in order to position the U.S. for growth and leadership in the global marketplace.
David Bem is vice president, science and technology, and chief technology officer at PPG.
Copyright 2024 Nexstar Media Inc. All rights reserved. This material may not be published, broadcast, rewritten, or redistributed..