One supply-chain solution: Automate the jobs we can’t fill

This fall a huge supply-chain story dropped as quietly as a tree in the middle of the woods: Singapore launched a new port in Tuas that officials say will eventually be able to handle more cargo every year than all U.S. ports combined. The secret to its prolificacy? Automation.
This might scare some workers out there, but the reality is that the global supply chain has been deeply disrupted by the pandemic and the “Great Resignation” of employees across the globe. The country is suffering. At one point this summer there were 5.5 million vacancies in the U.S. job market alone, with particularly pronounced impacts for air travel, manufacturing, warehousing and logistics. In trucking, for example, a 2021 analysis of 26 economically-advanced countries reported 2.6 million open positions, a number that’s expected to grow further in 2022.
Given how vital these sectors are to the global supply chain, it’s no surprise that their labor shortages have been so disruptive. Flight delays and cancellations are at their highest level in modern history. Major ports still regularly report days-long queues for unloading shipping containers. Rising inflation, increasing freight costs and a shortage of dock workers have spurred months-long delivery delays for furniture and other consumer goods. The Biden administration’s recent efforts to reduce the U.S. shipping log-jam have been stymied by the fact that there simply aren’t enough truck drivers or warehouse workers to meet demand.
Companies are scrambling to get things running more smoothly with everything from production and inventory management to transportation and distribution. Amidst this climate of setbacks and slowdowns, there’s a solution that will make workers’ jobs easier while also improving efficiency: leveraging technology and automation.
You might have heard a bit about automation lately, and not always for good reasons. Yet, lost amongst the endless parade of think-pieces about artificial intelligence (AI) stealing our jobs is the stark reality that the pandemic has inspired many laborers to opt-out of the dirty, dangerous or just plain dull jobs that they previously put up with. Our supply-chain crisis may not seem to show any signs of improving to date, but it could turn around if we got more creative in how we offer labor support in under-resourced industries.
The addition of more automation could start from the moment a good arrives at a distribution center. The movement toward e-commerce has actually created a fundamental need for more workers, not fewer: The role of picking and transporting merchandise has dramatically shifted from us in-person consumers browsing department-store aisles, to online sellers who are expected to ship things across the world in two business days. The shortage of warehouse workers is further exacerbated by the fact that this population is increasingly aging (and tuning) out. Without more help, employees will continue to be relied upon to work overtime and spread themselves thinner and thinner in what’s already an exhausting and stressful work environment, spurring burn-out and contributing further to the employment gap.
Automation in these settings doesn’t mean replacing employees, but developing more robust inventory management software and using systems like scanners and conveyors that make our jobs easier. Automation could be used to help transport pallets and perform a range of physical tasks. This would enable warehouse workers to focus on other more detail-oriented roles, from overseeing the operation of forklifts to improving the efficiencies of distribution centers. McKinsey consulting firm has cited technical skills in advanced IT and interpersonal skills like stakeholder communication as increasingly important in the areas of transportation, warehousing and manufacturing.
The logistical challenges continue after goods leave the warehouse and head to the trucks, ships, planes and other transit needed to deliver them. With trucking, labor shortages have grown due to factors like the profession’s low pay, high stress and grueling hours on the road. These challenges have also made it especially difficult to attract younger generations of workers. This is where automation can make the job less tiring and more appealing: Systems like PlusDrive can significantly improve fuel economy through its optimized breaking and accelerating methods, and also allow drivers to exert less mental effort during actions like lane-changing or the long hours they spend on the highway. (Amazon is in the process of starting to use PlusDrive in many of its trucks.) Fundamentally, automation reduces drivers’ workload and improves their work condition.
New technologies are also increasingly being used in some of the largest shipping ports across the globe. The recent concerns about automation raised by dock workers striking in cities like Los Angeles and Long Beach is understandable. At the same time, for decades ports have been among the places that have innovated the best: In the 1950s, docks started using huge cranes to move cargo, with the goal of sparing longshoremen from having to do such dangerous, back-breaking tasks by hand with nets and pallets. The latest wave of automation — with terminals that can load massive shipping containers onto trucks in just a couple minutes — is what many top port officials have cited as the reason they can now handle the “historic volumes” that have emerged in recent years. As ships and shipments get larger, automated terminals will fully evolve from being luxuries to necessities.
Aviation is another industry that, while embracing automation in some ways, still has a long road (or runway) ahead. A study from management consulting firm Oliver Wyman estimates that, without proactive efforts to train and retain pilots, the United States could have a shortage of 80,000 pilots within the next 10 years. Earlier this year, I recall landing at Boston’s Logan Airport late at night and having to wait four hours before the plane could taxi to the gate, due to the fact that there were five different planes to be moved and only one pilot left who could complete the task. In a world where self-driving cars have logged hundreds of millions of miles in complex, congested environments, it’s realistic to assume that we can harness some of the same technologies to tasks like taxiing airplanes.
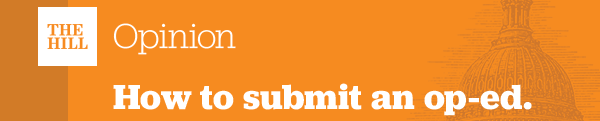
Getting people used to the idea of more automation will be no easy feat. Workers don’t feel valued by their employers, so throwing new routines and scary-sounding tech at them certainly has the potential to alienate them further. Because of this, it’s vital that companies discuss these changes while proactively prioritizing workers’ professional development and growth within the organizations. If employees can see a path for meaningful career advancement, the notion that automation will be used for some of their responsibilities — including the more menial ones — is likely to be far less anxiety-producing.
Responsibilities, jobs and entire industries are always in states of transition, but it doesn’t help to stick our heads in the sand and hope that the waves wash ashore. Automation can help reduce employees’ workload and improve their environment and conditions so that they feel more energized and less stressed.
Daniela Rus is the director of MIT’s Computer Science and Artificial Intelligence Lab.
Copyright 2024 Nexstar Media Inc. All rights reserved. This material may not be published, broadcast, rewritten, or redistributed..